4 ways of storing hydrogen from renewable energy
by Admin
Posted on 23-06-2023 04:51 PM
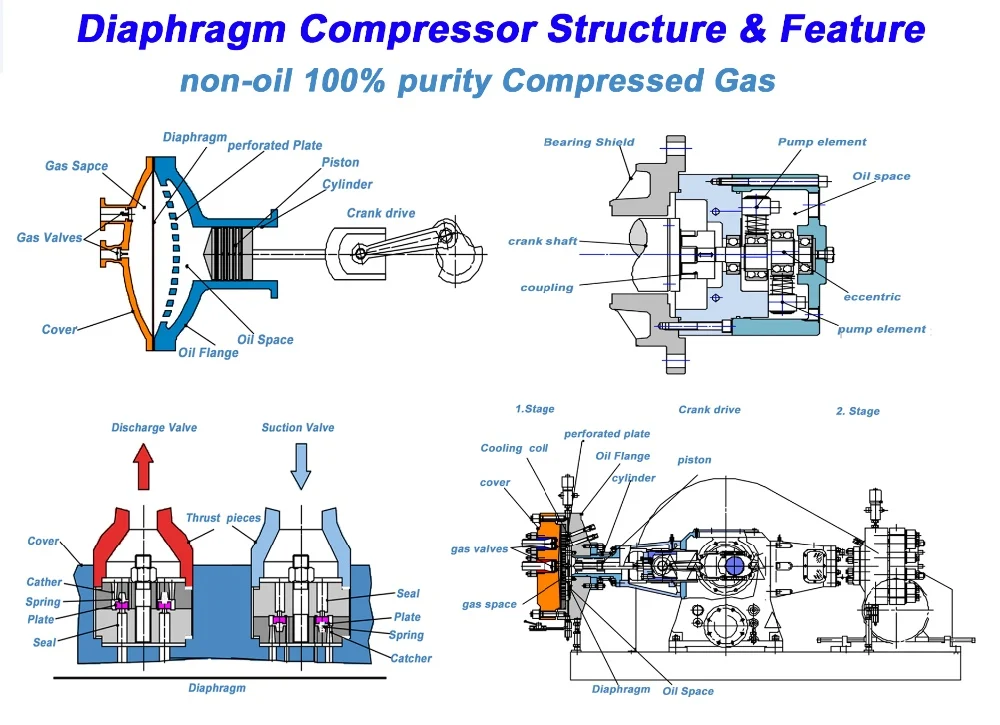
As hydrogen’s potential as a clean, renewable and scalable energy source is becoming clear, there are differing opinions in the market over the optimal way to store the large volumes of h2 needed for various power applications. Hydrogen is the lightest, and arguably the most powerful, element of all.
Considering these two facts, the challenge of providing a significant amount of hydrogen to a fuel cell or combustion engine starts. Therefore, it needs to be stored at high density in order to contain enough fuel within a feasible space to drive a fuel cell in a mobile application like a truck or a train.
By laura pérez | feb 10, 2022 | technical articles how is hydrogen stored? the following article reviews the different ways in which hydrogen can be stored and its current development status. Hydrogen will not be produced on-site and at the time of its consumption for many purposes. Instead, hydrogen can be produced at a central site and stored for further end-use distribution. Therefore, storage and/or transport systems are needed throughout the renewable hydrogen chain. The most suitable storage vessel will be determined by the use of this storage, the volume to be stored, the length of storage, the required discharge rate, the geographical availability of different options and whether the storage is small-scale or large-scale.
Why is hydrogen energy storage vital?
Hydrogen-powered vehicles are becoming more and more popular. Hydrogen fuel cell passenger vehicles, buses, and scooters are popular alternatives to gas or diesel-powered models. Hydrogen-powered forklifts and power machinery are also becoming more common. Hydrogen compressors can compress fuel into convenient storage cylinders for transport to refueling centers, and can also be used in the offloading and filling stages.
Compressed hydrogen can be used throughout the renewable energy industry, including to compress synthesis gas or syngas.
For storage and transport of hydrogen exist a lot of different possibilities. For small amounts of hydrogen metal-hydride storage or liquid organic hydrogen carriers (lohc) can be used. The principle is that hydrogen under medium pressures is bound to a carrier material and can be released when needed via an endothermal process. Another storage and transport method used is in the filling of pressure vessels such as cylinder banks or tube trailers. For the transportation of big quantities from 10,000 to 1,000,000 nm3/h of hydrogen, pipelines of corresponding diameter and operating pressure are suited best. They also offer a significant storage capacity.
Linde has been harnessing the power of hydrogen for over 100 years and is the global leader in the production, processing, storage, and distribution of hydrogen. Hydrogen is the most abundant element in nature. Even though it is the simplest molecule (consisting of two protons and two electrons held together by electrostatic forces) hydrogen is a powerful energy carrier. Today hydrogen is primarily manufactured industrially by conventional steam methane reformation (smr) of hydrocarbons or partial oxidation of carbon-based energy sources. With the growth and availability of alternative, low carbon-based energy sources, in combination with low carbon production processes, industrial quantities of hydrogen can be produced with a low carbon intensity.
Where next for hydrogen storage?
Hydrogen refuelling stations typically take gas hydrogen from a source, whether that is an electrolyser at low pressure (typically around 30 bar), pipeline at low to medium pressure (typically 50-80 bar) or supplied by a compressed hydrogen delivery asset at medium to high pressure (typically 200 bar to 500 bar). In all cases, the hydrogen usually needs to be compressed further to the required pressure, ready for refuelling, and held in local storage units. The lower the supply pressure, the greater the requirement on the compression to boost the pressure up to the required refuelling pressure. There are two main pressures that that are most common in the industry, 350 bar and 700 bar.
Technical report ahluwalia, r; hua, t; peng, j;. On-board and off-board performance and cost of cryo-compressed hydrogen storage has been assessed and compared to the doe 2010, 2015 and ultimate targets for automotive applications. The gen-3 prototype system of lawrence livermore national laboratory was modeled to project the performance of a scaled-down 5. 6-kg usable hydrogen storage system. The on-board performance of the system and high-volume manufacturing cost were determined for liquid hydrogen refueling with a single-flow nozzle and a pump that delivers 1. 5 kg/min of liquid h{sub 2} to the insulated cryogenic tank capable of being pressurized to 272 atm (4000 psi).
Higher volumetric storage capacity than compressed gas fewer evaporation losses (boil off losses) than in typical compression mechanisms or liquid hydrogen cryo-compressed can be denser than liquid hydrogen – cryo-compressed hydrogen can be in liquid or gaseous state. The dormancy is greatly extended as the allowable pressure inside the vessel increases.
Solution: diaphragm compressor application: h2 generation and compression on site for the hydrogen filling station the pressures of 30-100 bar generated by a pem electrolyser have to be compressed to the necessary 700 bar to refuel vehicles. The mre 300 diaphragm compressor could be used for this application. The hydrogen is compressed in two process steps, initially to 300 bar and then to 935 bar in high-pressure buffer storage. The refueling is then carried out from the "cascaded" storage. In this so-called tank cycle, 300 bar are initially poured into the vehicle tank. The tank is then filled from the 935 bar until the car tank has the required 700 bar.
Various refrigeration techniques may also be employed. This includes cryogenic cooling where subcooling units convert compressed, gaseous hydrogen into a liquid. By reducing the ambient air temperature below freezing, easy delivery of hydrogen is possible. While high-pressure hydrogen storage is preferred for use applications, liquid hydrogen is more efficient for large-volume transport. The nash liquid ring compressor is simple with only one moving part that is a rugged, balanced rotor requiring no internal lubrication. A rotating ring of liquid compressant does what sliding vanes or pistons do in other compressors. Understanding how each method works can help determine best practices depending on specific application needs.